
SATS
(Small Aircraft Transportation System)
and the role of
Meyers Aircraft Company

The SATS initiative (Small Aircraft Transportation System) is
being developed as a result of the AGATE (Advanced General Aviation
Transportation Experiments) program by NASA and leading industry
companies. NASA has been tasked with overseeing the project and has been
providing funds for joint research and development to private companies.
This extraordinary program is the first government funding for the light
aircraft industry in recent history, maybe even before WWII. The following
analysis and conclusions draw heavily upon the recently (July 1999) published
NASA AGATE/SATS information and is crucial to understanding the future of light
aviation. Many Adobe Acrobat pdf files are presented herein with links for
those whose browsers do not support plug-ins. There is a lot of
information here, so please be patient. It says it could take 795 seconds
to load at 28.8 kbps.

The
Challenge

Basic
Goals
The basic goals of the AGATE program can be summarized below:

Organizational
Structure
To understand where SATS fits into the general scheme of the
program's structure, an understanding of the following chart is necessary:
States
Involvement
Here is a quote from the
article contained in the Market Forecast
section;
"Although SATS evolves out of Agate, he
said, the four-fold increase in speed does not come from the vehicle
so much as it does from smart planning and point-to-point routing.
"The follow-on program to that effort, which exploits the
positive things done by Agate, is SATS," according to McHugh.
"We have at least eight states that are committed to bringing
money to the table to do local infrastructure planning within the
states."
And the actual signed Resolution:
Thus it can be seen that the SATS program is part of the final
stages resulting from the implementation of technologies derived from the AGATE
program. The entire effort is a joint effort between NASA, FAA, States and
US Industry.

Interdependent
Programs
And finally, the SATS program depends on using technologies derived from the
other programs such as NAS Infrastructure, Cockpits, Training, Airframe and
Propulsion.

SATS
Presentation
The following link will enable you to view the entire SATS Overview
as presented by Dr. Bruce J. Holmes in June of 1999. The file is large (almost 2 mb) so
you may skip to the conclusions presented below or peruse the original presentation as
one wishes.

Specific
Aircraft Capabilities
From the presentation entitled State of the Art: Avionics, (to
see the entire presentation, Click
Here) there is a slide depicting clearly what the SATS aircraft
of the "future" would be capable of in terms of performance and range.
The above slide appears as the last of 35 pages in the Avionics
State-of-the-Art presentation and apparently signifies the goals to be achieved
in terms of the actual aircraft by 2007. To reiterate, these are:

To see how well the Meyers 200D relates to these stated
objectives for the year 2007, one must first go into numerous other SATS
documents and other AGATE sources to attempt to define the meaning of the above
goals according to the authors.
Let's take each goal and attempt to do an analysis and make
comparisons. Management is going to state from the outset, that the
following will prove that the Meyers 200D is one of the very few, if
not the only, SATS qualified aircraft currently available.

Currently, there are no FAA crashworthiness standards for
aircraft. Aircraft are supposed to fly, not crash. If one builds an
aircraft like a tank, it would be too heavy to fly with available engines and
would fall completely outside of the program performance/cost guidelines.
Therefore, better engineering is the answer or at lease better types of
construction.
The differences between aluminum and composite construction will
be further discussed below under affordable, however some issues of
crashworthiness need to be addressed. While composites may be stiffer than
aluminum and more crashworthy than conventional semi-monocoque construction,
they are certainly not equal to the Meyers 200D in their current
configurations. Perhaps a look at state-of-the-art in automobile racing
would be appropriate. NASCAR has very complete and inflexible guidelines
when it comes to construction of the automobile chassis for safety
reasons. The pictures below illustrate this principle:
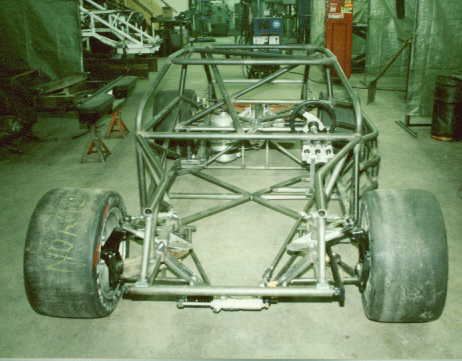
|
This is a typical chassis showing the tubular steel construction prior
to the body panels being placed in position. This construction is
absolutely mandatory to protect the drivers at speeds of around 200 mph
and is inspected and must pass NASCAR specs prior to being allowed on
the racetrack. |
This is a NASCAR frame being assembled in a welding jig
to keep the frame true and exactly positioned. |
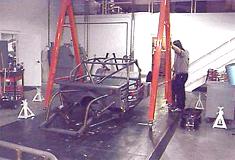 |
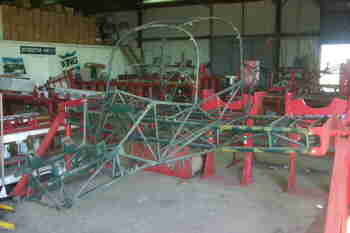 |
Here is the main 4130 chrome-molly steel assembly consisting of the
engine mount, center section and cabin section. The pilot and
passenger actually sit on the large steel bar running through the
cabin, which is the top piece of the main spar. The seat belts
are attached to the steel both front and rear and the shoulder harness
attach-points are contained in the overhead steel structure which also
doubles as the two roll-bars. The center section is about 10
feet wide. There is more steel in the Meyers 200D than in a
NASCAR chassis. |
Here is the Meyers 200D cabin section in its welding
jig. |
 |
Here is the Meyers 200D center section in its jig. |
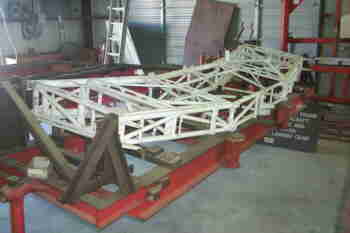 |
Now, hopefully, your aircraft will never be involved in an
off-airport landing. But in the very unlikely event that one is, what
type of construction would you prefer to have surrounding you and your
passengers?
To be truly affordable, the economies of scale
will certainly have to come into play as well as new design techniques.
Basic materials selection is also of paramount importance. Management will
provide excerpts from various AGATE and SATS articles below to illustrate
several issues. The main disagreement Management has with the entire AGATE
program is their seeming fixation on composite materials as the construction
medium of the future. We disagree. Allow us to first look at NASA's
published data regarding basic materials as taken from the automobile industry:
Basic
Material Selection